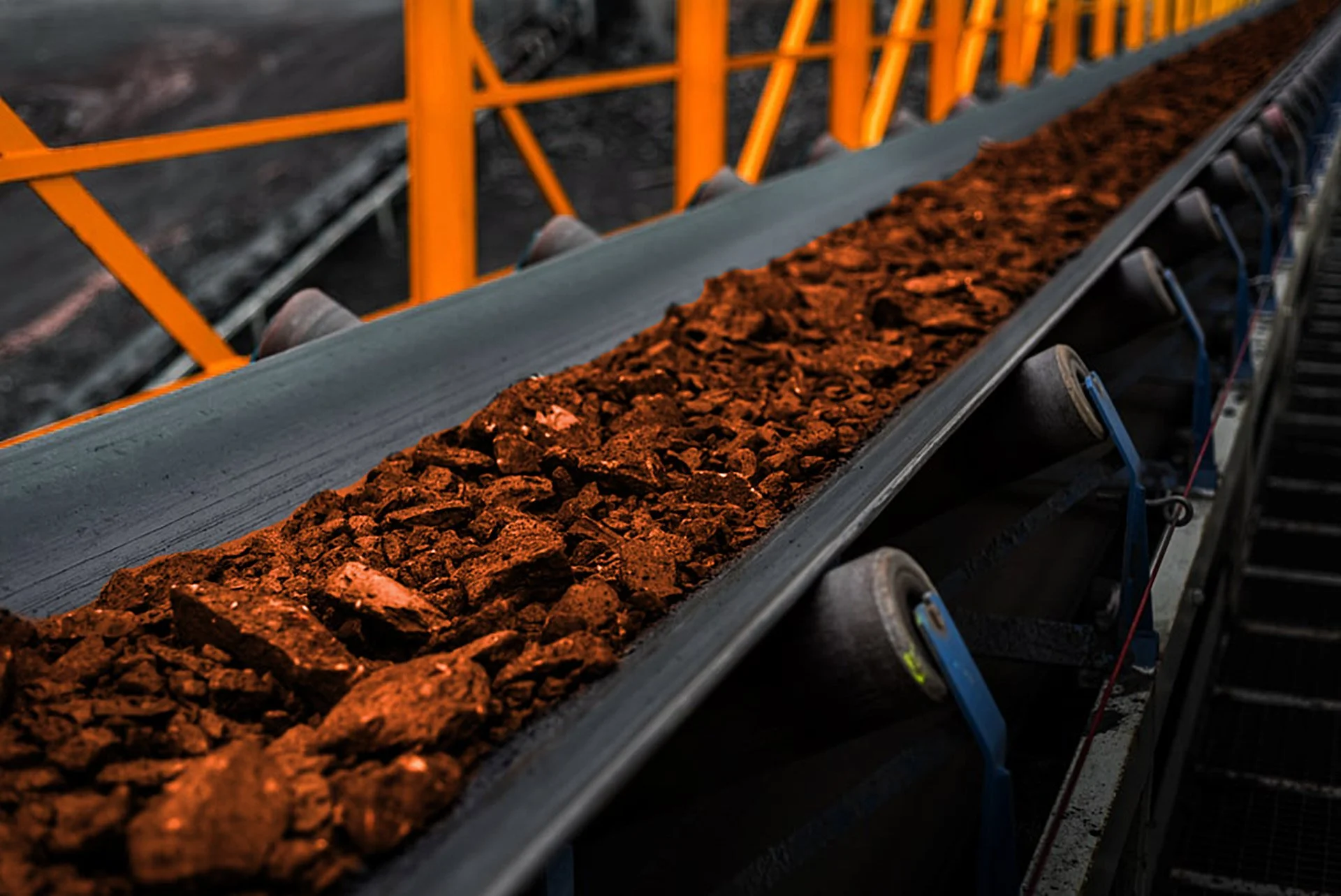
Case Studies
Industry Solutions
Underground Mining Boom Buffers and Hose Reels are manufactured for resellers.
A heavy-duty installation required new inserts for the drive coupling between a 5mW motor and gearbox. Polyurethane Processors designed and manufactured inserts of a suitable hardness and flexibility.
A Major Queensland Mining Company was experiencing problems with material build up in Discharge Cones requiring down time to remove the blockages. Polyurethane Processors were able to formulate and apply smooth and slippery Hot Cast Polyurethane Linings to eliminate the problem.
Agitator Blades used in the Gold Mining Industry were being lost due to failure of the mounting bolts. Bolt failures were caused by Hydrogen Embrittlement from interaction with slurry chemicals. Polyurethane Processors designed and produced Bolt Protection Kits, comprising of Polyurethane Caps for bolts and nuts, plus sealing materials, and primers. This allows site workers to completely seal the mounting bolts, preventing wear and breakage.
An Organisation which provides services for disabled people requested our assistance. They had developed a mobility device to allow disabled people access to the ocean for therapy. This required wheels suitable for operating on car parks, footpaths, ramps, beach sand and also able to enter the water. Pneumatic tyres were not suitable for safety reasons. Flexible wheels fabricated from stainless steel had been used in the past with some success but also had problems;
Noisy on hard surfaces
Sand penetration of riveted joints
Sharp edges which could injure the patient and helpers
We were requested to provide a Polyurethane Coating to alleviate these problems. This was not feasible for several reasons.
Polyurethane Processors proposed designing and casting wheels from a suitable grade of Hot Cast Polyurethane. In order to keep weight down the wheels were designed with a flexible outer rim and flexible spokes. We were also able to discard the original steel hub and bearings, making the hub an integral component of the wheel, designed to accept thin wall bushings instead of bearings. This resulted in a wheel lighter than the original item with no metal hub, better on all surfaces and not affected by sea water. Unfortunately, our participation in this project was cut short for commercial reasons.
We have gained satisfaction from knowing that Polyurethane Processors have the ability to recognise a situation, provide a solution, design and manufacture complex moulds, devise casting and curing methods and also machine finishing and fitting of special bushes. The mould has been made with reversible segments, suitable for casting right hand and left hand wheels.
Case Studies
Customised Components
A major heavy equipment supplier used steel yard rims to move heavy dump trucks and front end loaders around the premises prior to delivery. Due to the heavy load the steel rims were damaging the concrete in the yard and workshop. Polyurethane Processors cast Polyurethane tyres on to the steel rims – RESULT no more concrete damage. These tyres operated for more than 18 years before any re-working was required.
Since 1995 Polyurethane Processors have refurbished wheels and sprockets for rubber tracked vehicles used by Drilling Companies on soft and boggy ground. These conditions result in heavy wear on track tyres. The drive sprockets are prone to failure due to de-bonding of Polyurethane from the steel hub. Polyurethane Processors modify the hubs to prevent de-bonding of the new Polyurethane.
Western Australian Hospitals are equipped with portable x ray machines running on wheels fitted with Polyurethane tyres which are prone to failure. Polyurethane Processors are engaged in a programme to replace these tyres with a more suitable Polyurethane product. The wheels are brought to us in sets, we strip failing Polyurethane, recast new tyres and machine finish. We have treated many of these wheels over several years. None of our wheels have ever needed to be re-furbished.
Polyurethane Processors were asked to reline large valves which use a ball to seal alternative inlets.
The initial valve body and lid were previously lined by another company using Hot Cast Polyurethane with ceramic tiles bonded in to high wear areas. Ultra-high pressure water from our Hydro Knife Equipment was utilised to strip out worn linings. It was noted that the existing lining was partly de-bonded.
When casting the new lining, extreme care was taken to ensure full bonding was achieved.
Associated pipework was also stripped and relined, partial de-bonding was observed in these items also. Debonded linings can suffer failures allowing sections of lining material to become detached, which can cause a blockage and shut down the plant.
Polyurethane Processors, thorough surface preparation, casting and curing procedures prevent bond failures.
Case Studies
Customer Feedback
Hot-cast polyurethane conveyor pulley lagging has been carried out by Polyurethane Processors since 1985. In this time, no premature failures have been reported. Procedures include surface preparation, casting, oven curing, machining and cutting of diamond pattern grooves, all done in-house. The polymer and curative is mixed and dispensed by machine, great care is taken to ensure correct mixing ratios and temperatures are maintained. These pulleys are mostly destined for major iron ore mining operations in Western Australia, some other applications have included ship loaders in Queensland.
Advantages of hot-cast premium grade polyurethane lagging:
Significantly longer life compared to rubber lagging.
Less likely to cause damage to belts which can occur with ceramic lagging.
Polyurethane is machine finished concentric with bore of pulley.